Sameer Sah, Partner and Varun Narayan, Senior Associate at Khaitan & Co highlight the need for a risk management framework in place to focus on evaluation of potential issues arising from the loss of a supply chain partner or location
As countries and companies alike continue to grapple with the unprecedented challenges thrown up by the novel coronavirus (COVID-19), a specific area of concern has been the uncertainty surrounding the impact of the COVID-19 pandemic on the global as well as Indian pharma industry supply chains. The concerns have been aggravated by the fact that COVID-19 struck first, and worst, in China, which is the world’s leading producer and exporter of active pharmaceutical ingredients (API) by volume. A significant number of pharma companies in India and around the world import a bulk of their raw materials from China, which witnessed a lockdown of over two months from January 2020 to March 2020, while it battled COVID-19.
To understand the significance of China’s role in the global pharma industry, one need not look beyond India’s shores. The Indian domestic pharma industry is highly dependent on imports, with more than 60 per cent of its API requirements being imported. Of the total imports of APIs and intermediates into India, China accounts for nearly 65-70 per cent. In some specific APIs, like cephalosporins, azithromycin and penicillin, the dependence is as high as 80 to 90 per cent. It is more alarming in case of intermediates of stages prior to APIs and key starting materials (KSMs) which are the building blocks for drugs, wherein, in some cases, China is the exclusive supplier. For instance, PenG and 7ACA, the key raw materials required for manufacturing cephalosporins are sourced exclusively from China. Additionally, for some input materials, even if alternate sources are available, China remains the preferred source given the economical rates.
While the lockdown of manufacturing operations in China has raised concerns globally, major pharma manufacturers have said in statements that they are closely monitoring their supply chains and do not anticipate near-term shortages. However, most of them noted that if COVID-19 persists for prolonged periods, the situation could change. Certain Indian companies have also stated that the country’s big pharmas are currently well-stocked and that the larger Indian pharmaceutical companies have stocks that will last them for up to six months. However, according to ICRA, the domestic API manufacturers typically have an inventory of one to two months, which should adequately support their production till mid-March 2020. Continuation of the COVID-19 outbreak, however, beyond mid-March 2020, may adversely impact production of these API manufacturers, possibly leading to a complete halt of production for some smaller players, according to ICRA.
While most pharma companies have been able to successfully withstand the lockdown of factories in China, as they have inventory on-hand to offset short term supply interruptions, any impact on the supply chain may truly only be felt if, the impact of COVID-19 persists beyond mid-April.
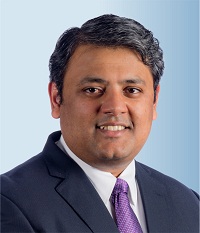
Although the impact on the pharma supply chain persists, pharma companies are currently drawing comfort from a few confirmed news reports claiming that Chinese factories have restarted operations and are ramping up their production steadily. Additionally, logistics’ chains seem to be de-clogging and re-opening. At the same time, pharmaceutical manufacturers still need to prepare for the fact that Chinese factories may take time to reach peak production capacity. As an alternative, domestic players can consider sourcing APIs and intermediates from other countries, albeit at higher price, which in turn may have a knock off effect on prices in India – bear in mind that European countries are not strangers to the brunt of this virus. The Indian government, in its efforts to ensure uninterrupted availability of critical APIs, has restricted the export of 26 APIs and finished pharmaceutical products till further notice. It has also prohibited the export of surgical /disposable masks and ventilators to combat the acute shortage of such equipment.
The COVID-19 crisis has highlighted the importance having a risk management framework in place that focuses on evaluation of potential issues arising from the loss of a supply chain partner or location. Having alternate supply arrangements, to the extent possible from a quality perspective, reduces potential disruption while ensuring adequate stockpiles provides a buffer against temporary turbulence.
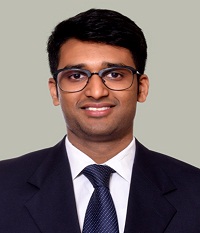
Some legal considerations
- Operational continuity at manufacturing facilities and employee health: As of now, the central government has ordered a complete lockdown of all commercial activities (except some essential establishments like pharmacies, hospitals, etc.) across the country and introduced unprecedented social distancing measures to curb the spread of COVID-19. All manufacturing facilities, other than those manufacturing essential goods, have been ordered to shut down. Pharma facilities, however, have been exempted from the lockdown for obvious reasons. Nevertheless, pharma companies must set up adequate infrastructure to screen all of their workers and take all other required precautionary measures to ensure that their facilities and workers remain uninfected. In light of the continued operations of its facilities during this period, pharma companies would also be subject to additional risks as ‘employers’ and would have to prepare themselves for safeguards to ensure health and safety of its employees.
- Notifications to the National Pharmaceutical pricing Authority (NPPA): Pharma companies manufacturing scheduled formulations under The Drugs (Prices Control) Order, 2013 (DPCO 2013) must carefully monitor their output levels. If any pharma manufacturer needs to discontinue manufacture of any scheduled formulations due to the unavailability of APIs, the same needs to be notified to the central government in accordance with DPCO 2013 provisions. The central government, may, in public interest, direct other measures. Also, manufacturers of scheduled formulations need to be conscious of prices where ceiling prices have been notified. Separately, manufacturers of non-scheduled formulations cannot increase the MRP of the drugs manufactured by them more than 10 per cent of the MRP during the preceding 12 months.
- Force majeure clauses in existing supply agreements: The lockdown of manufacturing facilities by the Chinese government has caused a drastic reduction in supplies coming out of China in the last two to three months, and these worries were compounded by breakdown of logistics’ chains as well. This has the potential to cause knock-on effects on a large portion of pharma manufacturers, some of whom may be beginning to experience problems. Many manufacturers could be staring at scenarios where they are unable to honour minimum supply commitments or are on the verge of defaulting on orders, for reasons beyond their control. Against this backdrop, such companies may consider invoking ‘force majeure’ clauses in their supply agreements to deal with supply chain disruptions caused by COVID-19. A force majeure event occurs when unforeseeable circumstances, such as natural catastrophes, epidemics and pandemics, prevent one party from fulfilling its contractual duties, absolving them from penalties for duration the force majeure events persists. Having said this, companies must carefully evaluate the actual language of the force majeure clauses in agreements before deciding on any future course of action. In our experience, most clients are evaluating these provisions, but we are not necessarily aware of people having issued notices, given the overall criticality of the industry. Companies also need to consider that the invoking or not invoking of the force majeure clause will have a reputational impact as well, post the crisis tiding over.
Conclusion
Global supply chains are set for a major overhaul as the COVID-19 crisis has exposed the vulnerability of countries and companies that rely heavily on a limited number of trading partners. Many multi-national companies (MNCs) have already started re-evaluating their supply chains and are in the process of shuffling their supply chains to reduce concentration in a handful of countries.
The COVID 19 outbreak has also presented Indian pharmaceutical companies an opportunity to become a preferred alternate hub for manufacturing APIs and intermediates. Having recognised this opportunity and declaring Indian pharma’s dependence on Chinese APIs a threat to national security, the central government has approved a slew of measures to promote manufacturing of APIs and KSMs within the country. This includes approval of Rs 3,000 crores project to set up three bulk drug parks in coordination with three states, as well as a 20 per cent financial incentive for the next six years for manufacturers to make 53 critical bulk drugs, which are in turn used to make medicines. The scheme is expected to reduce manufacturing cost of bulk drugs in the country and dependency on other countries for bulk drugs. This incentive from the central government and the lessons from COVID-19 are with a hope to change the global footprint of Indian pharmaceutical companies and more importantly, reduce dependence of the domestic pharma companies on a single supplier like China.