Perlen Packaging revolutionising dry powder inhalation
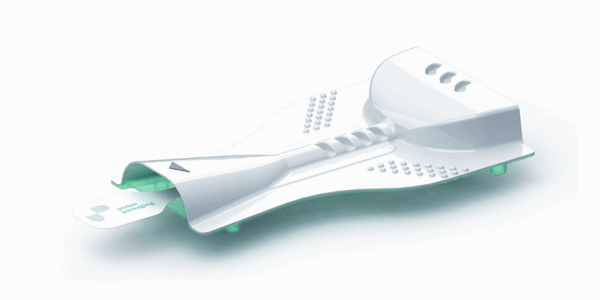
Matteo Trisoglio, Manager Business Development, Perlen Converting, gives an insight on PERLAMED-BLIST, which has a simple design with low manufacturing cost
Since the invention of the multi dose, dry powder inhaler back in the 50s the API´s are administered in multi dose devices that are quite complex. This complexity requests patients to be skilled on their devices, not ideally for disposable and/ or single use applications and, furthermore, requests high manufacturing costs. Perlen Packaging presented during the Pharma-Pack 2017, in Paris, the world’s first thermo-formed Inhaler (BLISTair).
Advantage of the products

The thermo-formed packaging is protecting the device itself throughout a high barrier film that Perlen is selling since years in the market with comparable barrier efficiency like Alu-Films that are in use for such applications. On one hand, the thermo-formed packaging is protecting the powder and at the same time, the packaging is the device itself.
The handling of this device is extremely intuitive, there is simply to pull a lash of the device to open up the powder chamber and inhale the API.
For this reason, for the first time, a disposable single use inhaler is available to the market, without a need for a secondary packaging. The primary packaging is already the device!
The fields of applications are extremely wide. The requests Perlen has since first presentations are so wide, it starts from asthma/ COPD to vaccines, over to emergency and/or military applications as well as pain and cold treatments (OTC).
Obviously, the correct defined amount of inhalations, given by the nature of this system, allows running perfect clinical trials with a set number of inhalations. As well as an application dedicated to a fixed period of time, limited inhalation period (E.g. in hospitals) the ‘BLISTair’ find its market. Lung cancer applications, palliative medication pain cold and OTC could be ideally administered in the case of ‘BLISTair.’

Compared to standard multi dose devices the single-use disposable device has a very flexible application field. A defined amount of inhalation, prescribed by a doctor could be sold in exact the prescribed amount and will help insurance companies to save money and contribute as well to save the environment. Instead of purchasing 30 or 60 inhalations, when 15 are needed the patient will have exact the needed amount, the health insurance will refund the exact amount and material and manufacturing is dedicated to the correct purpose.
‘BLISTair’ was tested, and is positioning itself, in a direct comparison, as very efficient. Trials realised with prototypes are proving very good results in particle distribution and in the device resistance. The device resistance, due to its flexible manufacturing process and the given flexibility of the system itself, is even adjustable. The emptying of the device is what specialists would call ‘complete’ and all results are definitely replicable.
Interesting aspect are the changes for PERLAMED-BLISTair in the so called ‘pharmeging countries.’ Those areas are suffering under pollution driven by the growth of their markets and with this, the amount of potential patients is rising through the top. On the other hand, exactly this sector of (potential) patients cannot afford to pay 30 or even 60 inhalations, given by existing systems, at once. The patient should pay the amount of inhalations he is getting with the device. That’s where Perlens device is creating many requests, simply because by lowering down the single inhalations (manufacturing) costs, this segment of patients can purchase every single inhalation exactly in the corresponding size of their own wallet.
When it comes to evolved markets, we have to state that PERLEMED-BLISTair can add a value to existing Asthma and/ or COPD applications simply by improving the life-quality of patients. The device is so small that any stigmatisation of patients using a device is avoid. The device disappears, in a neutral flow-pack; with this any inhalation disappears literally in the hand of the patient.

By travelling for only two days, e.g. the patient can carry in his pocket only two BLISTair devices instead of a huge device and amount of blisters/ capsules. Why is this so? Because the primary packaging is the device.
If there is a need for a short-term inhalation such as for pain and cold issues (OTC), one can assume a treatment period of approximately 14 days. That approximately is the amount of inhalations within the BLISTair is pricewise almost unbeatable, according to Perlen.
Considering that point that the BLISTair can also offer a DUAL CHAMBER (so called ‘Tandem Version’) this device is seriously a revolution. The dual chamber gives the chance to combine two not registered API’s on ONE device and with this reduce the time to market and offers a full range of new applications to patients and pharmaceutical companies. In addition, two not combining, unstable API´s can now be administered simply by placing them separately within the same device until the patient pulls the lash and breathes. In this moment, the two API’s will be delivered together.
The impact on the environment is so low, that it makes it attractive also on this point of view. Considering that any transport and energy consumption for the manufacturing and device assembly is not requested, the CO2 Footprint of this device is seriously much more than a ‘green paint.’
The flexibility of this device is as well proven by the chances to administer the API trough the trachea, mucosa or lung and on two different ways: either oral or nasal. All of this on one and the same device.
Composition, how to produce and quality?
The complete manufacturing has been developed, from the beginning, with the cooperation partner of Perlen such as Uhlmann Pacsysteme GmbH and Harro Höfliger.
The project in terms of manufacturing is feasible and relay on existing, known and controlled, manufacturing processes of thermo-forming by Uhlmann and well-known filling from Harro Höfliger. Even sample manufacturing, studies, prototyping are realisable at very low costs. The barrier capabilities of the foils, containing the API, are available on the market since years.
Manufacturing costs are one of the main advantages the BLISTair is showing-off.
In cooperation with Uhlmann Pac Systeme and Harro Höfliger, Perlen Packaging worked out the realisation of this project and its feasibility. The solution is ready to go and today we can focus ourselves to see what the advantages of the BLISTair compared to an injection-moulded device.
First, we have to point out again that the PERLAMED-BLISTair gets along without any injection moulding at all.
This has the tremendous advantage that a pharmaceutical company is not depending on a third party, risks of transport, expensive toolings and dedicated warehouses for incoming goods as well as safety stock for injection moulded parts that are literally an equivalent to money placed under the matrasses.
Currently manufacturing requests, after the incoming components inspection, the assembly under big clean room conditions. All of those process steps and many others have been realised separately and under certain complications or challenges. At least at a certain amount of costs, to then finally have the marriage of all components to a DPI. In the case of BLISTair, the manufacturing is completely different.
The complete manufacturing can be realised at one site. Only all what is requested, is dedicated, but not newly invented, Uhlmann blister machine and the well-known powder-dosing unit from Harro Höfliger. The capacity of this machine is up to 300 devices per minute.
The material requirement for a yearly double-digit manufacturing is a few pallets of foils and for the packaging carton – that’s it. When it comes to adaptions on a device, the complete supply chain is usually involved. ‘BLISTair’ simply requires new blister machine tools. In the same period, a blister format is changed, in the same time and at the same costs, you turn the complete manufacturing to a different device and application.
Just by changing a format part on a blister machine. This is indeed revolutionary.
All of this, and more, are lowering the manufacturing costs dramatically and are simplifying the manufacturing of a DPI to a maximum. An assembly line is needless as much as a big cleanroom because the requested Uhlmann blister machine is much smaller than all assembly lines we all know. Furthermore, the blister machine — apologise — the device manufacturing machine is requesting less operators and controls. However, Perlen is launching this project with a tremendous offer: to act as a contract manufacturer for all those who are interested.
Advantages at a glance:
- Easiest adaptions to different powder formulations
- Oral and nasal application is available
- Drug delivery to the mucosa, trachea or the lung
- Adaptable designs
- Lowest manufacturing costs and low start investments
- Two powder chambers solution available
- Easiest and simplest supply chain
This all states that a new device is not a trial but can be a very simple step, taken by the motto ‘think outside of the box’. By using all what was already known and experienced in the market by the above-mentioned companies, Perlen Packaging created a new device with all the potential of a revolution, simply more than an innovation.
The Perlen Packaging BLISTair team states:
“…BLISTair underlines the innovation power of Perlen Packaging. Again we have proved that a specialization and courage will pay off…”
– Wolfgang Grimm, CEO, Perlen Packaging
“…Revolutionary. This true innovation can open up new segments and markets…not only to us in fact to all our customers!…”
– Johannes Giessler, CSO, Perlen Packaging
BLISTair is indeed a revolutioniser. With one single blister machine, DPI’s can be manufactured at lowest costs. The complete abstinence of injection moulding is self-speaking. This will allow many pharmaceutical companies to open up a market that was blocked in the past simply due to investment costs and to the spending capacity of patients in emerging markets.
– Matteo Trisoglio, Manager Business Development
- Advertisement -
Comments are closed.